Optimizing Agriculture’s Spare Part Production with 3D Printing
Agriculture is an essential industry that feeds the world’s population. The industry is highly complex and requires constant innovation and adaptation to stay competitive. One significant challenge that farmers and agricultural businesses face is ensure a high availability of their equipment, especially during the high season. When a machine breaks down, it can lead to significant losses in time and money, and finding replacement parts can be challenging. 3D printing is the game changer in this situation, and if used correctly, can significantly reduce lead times and costs.
Challenges in Agriculture Machinery
Imagine a farmer in the middle of a busy harvest season, working hard to ensure that the crops are collected on time. Suddenly, the combine harvester breaks down, and it’s clear that one of the parts needs to be replaced. The problem is, the manufacturer of the harvester no longer produces the required part or does not have it on stock and needs several weeks to provide it. The farmer is left with two options: either replace the entire machine or try to find a used or grey part from third-party suppliers, which may not be reliable or even available. This is a common problem faced by farmers and other industries with aging and/or complex machinery. The cost of downtime and replacement parts can quickly add up and affect the bottom line of a business.
The same goes for producers of those harvesting equipment. The older and more complex the product portfolio, the more difficult it becomes to maintain part availability for all versions. Often, parts come with huge minimum order quantities, leading huge inventories of often obsolete parts and wasting inventories of several millions per year – not cost-efficient and for sure also not sustainable.
Making spare parts available on-demand with 3D printing
3D printing offers a solution to the problem. It allows companies to produce objects in a timely manner without the need for expensive tooling or molds. Just a design is needed, and production can start. This helps farmers and equipment manufacturers overcome the challenges of obsolescence and downtime, as parts can be quickly reproduced on demand. Typically, long lead times, with an average of 3 month and more, thus turn into hours or days, keeping the farm running smoothly.
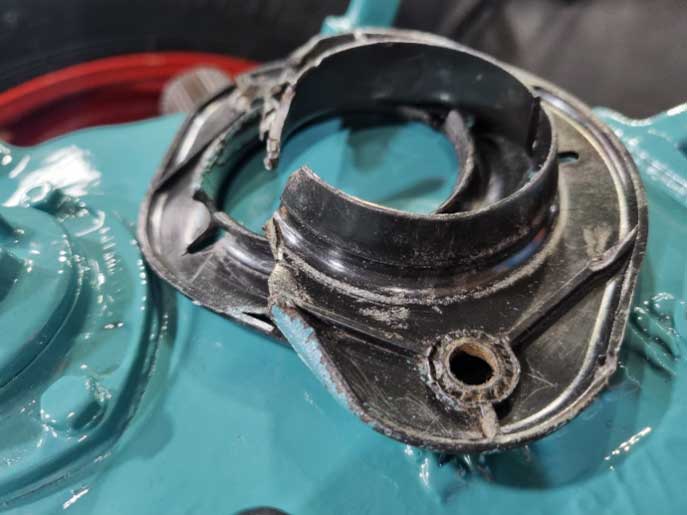
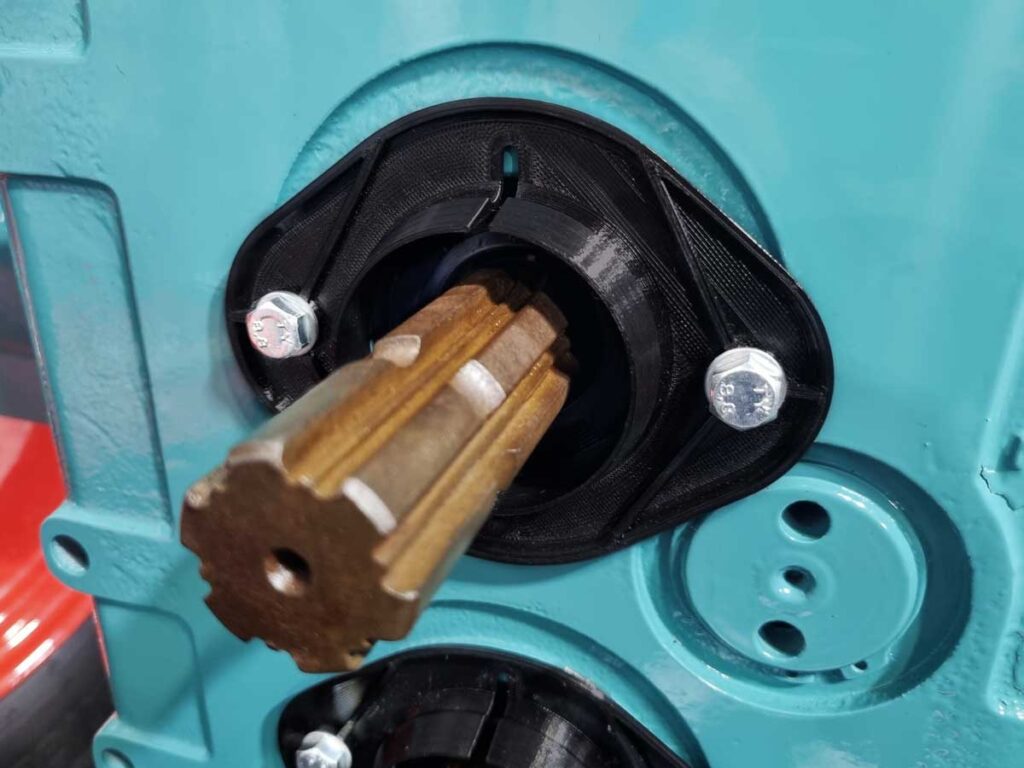
A PTO cover (left old, right 3D printed), which is traditionally no longer sold, can now be made available again within just 4:20 hours printing time using FDM technology with TPU64D material.
Producing from lot size one with a digital inventory
3D printing further offers the advantage of producing parts in small series and even single units more cost efficiently. This is ideal for the agriculture industry, where typically only small to medium series are required. Instead of storing large amounts of parts in warehouses, manufacturers of agriculture machinery equipment can store their part designs in a digital inventory. This can significantly reduce inventory costs and the risk of overstocking or understocking. So, parts can simply be produced when needed.
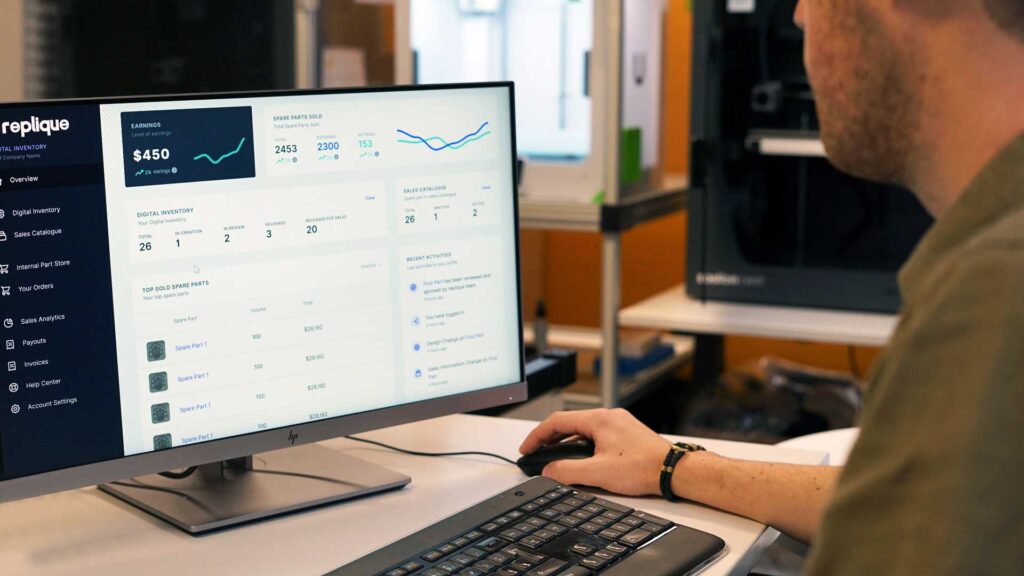
Making agriculture equipment more sustainable
3D printing technology is also beneficial for the environment. As mentioned, traditional manufacturing methods often involve a great deal of waste, as manufacturers need to produce more parts than necessary to ensure that they have enough inventory. However, with 3D printing, only the necessary parts are produced, reducing waste and helping to preserve the environment. As parts can be produced decentrally, it also reduces CO2 in transportation, if produced close to the location of the farmer. And lastly, it also makes farming equipment lasting longer with spare parts availability independently from the main product’s lifecycle.
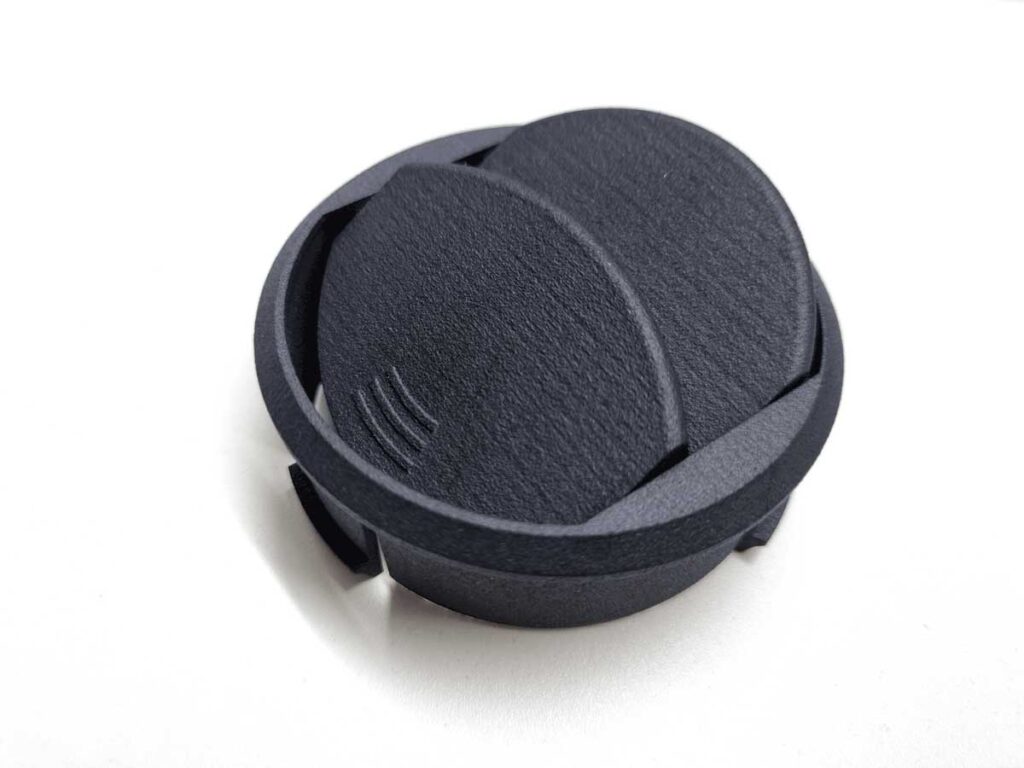
Typical injection molded parts can now be produced starting from lot size 1. Moreover, parts such as the air vent, which usually has to be assembled together, can be printed in one piece, saving time and money in production.
How to integrate 3D printing in the most efficient way
When it comes to integrating 3D printing in agriculture, there are three main options to consider, with the farmer integrating 3D printing, the farmer ordering the part via a 3D printing service, or the equipment manufacturer itself integrating the technology.
1. Farmer integrates 3D printers at the farm
The first option is for the farmer to purchase and operate their own 3D printer on-site to produce needed parts. While this option may seem appealing, there are some downsides to consider. Firstly, not all 3D printing technologies may be suitable for the farmer’s needs, and purchasing a printer that is not the right fit can result in a waste of time and money. Secondly, operating a 3D printer requires knowledge and skills that not all farmers possess, which may require additional training and investment.
2. Farmer orders parts from a 3D printing service/platform
The second option therefore is to order the parts from a 3D printing service or even over a 3D printing platform that has several 3D printing services located worldwide and close to the farmer’s location. This approach can provide farmers with access to a broader range of 3D printing technologies, materials, and expertise. Additionally, using a platform can enable farmers to quickly and easily obtain the parts they need without having to invest in a 3D printer and training. However, the struggle starts, when he cannot get a design of the part, as it is still in ownership of the manufacturer. This leads to the third option.
3. Equipment producer integrates 3D printing platform
The third option of integrating 3D printing in agriculture involves the hardware producers themselves adopting a 3D printing platform. This option provides the added benefit of the hardware producer having complete control over the design and quality of the parts produced.
To streamline the process, companies can integrate a digital inventory platform such as Replique. This allows them to store all their 3D printable parts in one place, already ready for production with fixed print parameters. When a farmer orders a part, they can place the order via their usual ordering system, such as a webshop or ERP system. This order is then processed in the digital inventory, triggering the printing of the part at the print farm. Once printed, the part is shipped directly to the end-user.
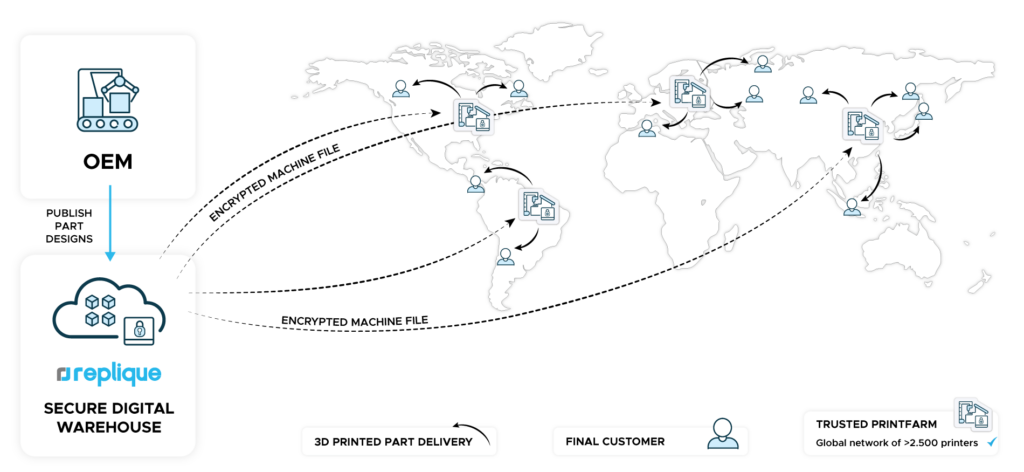
By adopting this approach, companies can quickly provide the necessary parts to their customers and so increase customer loyalty, without having to invest in own hardware and software. This option is of special interest for larger companies with a wide portfolio range and more extensive supply chains, where 3D printing can provide a more streamlined and efficient approach to part production and distribution.
Overall, all options have their pros and cons, and the choice of which approach to take ultimately depends on the specific needs and circumstances. However, for those who are new to 3D printing or have limited knowledge of the technology, using a 3D printing platform can provide a more efficient and cost-effective solution.
Categories
- 3D printing industries (6)
- 3D Printing Materials (1)
- Basics (3)
- News (1)
- Point of View (10)
- Press (20)
- Press (20)
- Sustainability (3)
- Technology (6)
- Uncategorized (1)
- White Paper (1)