3D Printed Small Series
Do you want to improve your market position and expand your product portfolio with small series and customized accessories?
Leverage the benefits of 3D printing and produce small series fast and cost efficiently – starting from lot size 1.
CHALLENGE
The production of small series is often not economical. Conventional production methods, e.g. injection molding, come with high investment costs for molds and models and require a long ramp-up time. Morever, for the launch of new products, no empirical data on future quantities is available, leading to high risk.
Expanding your product range for customers, however comes with many benefits, making it worth to look at more economical production methods:
- Stronger customer loyalty
- Additional business
- Preventing third-party suppliers from offering non-original parts of inferior quality, which can have a negative impact on your reputation
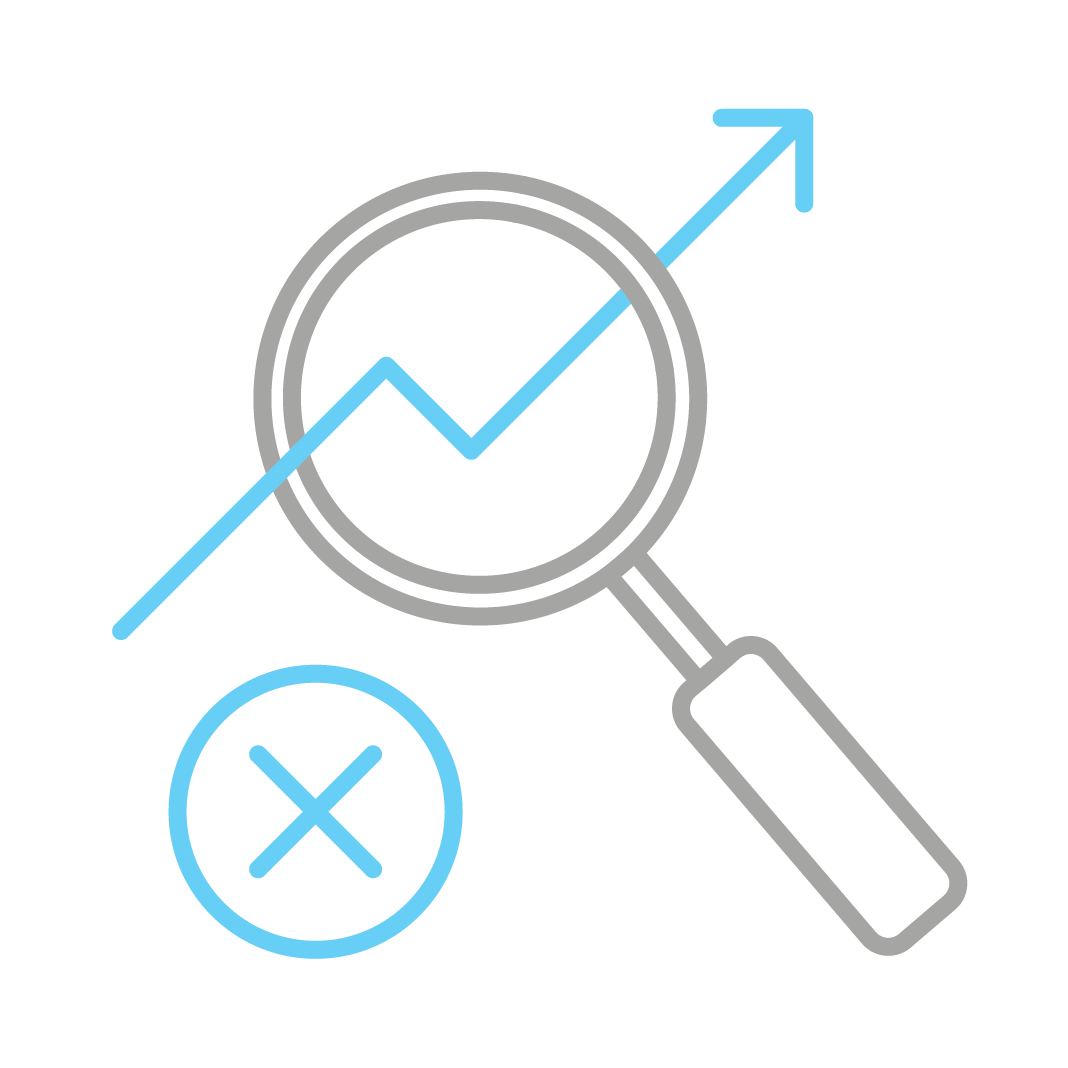
NO MARKET DATA FOR NEW PARTS
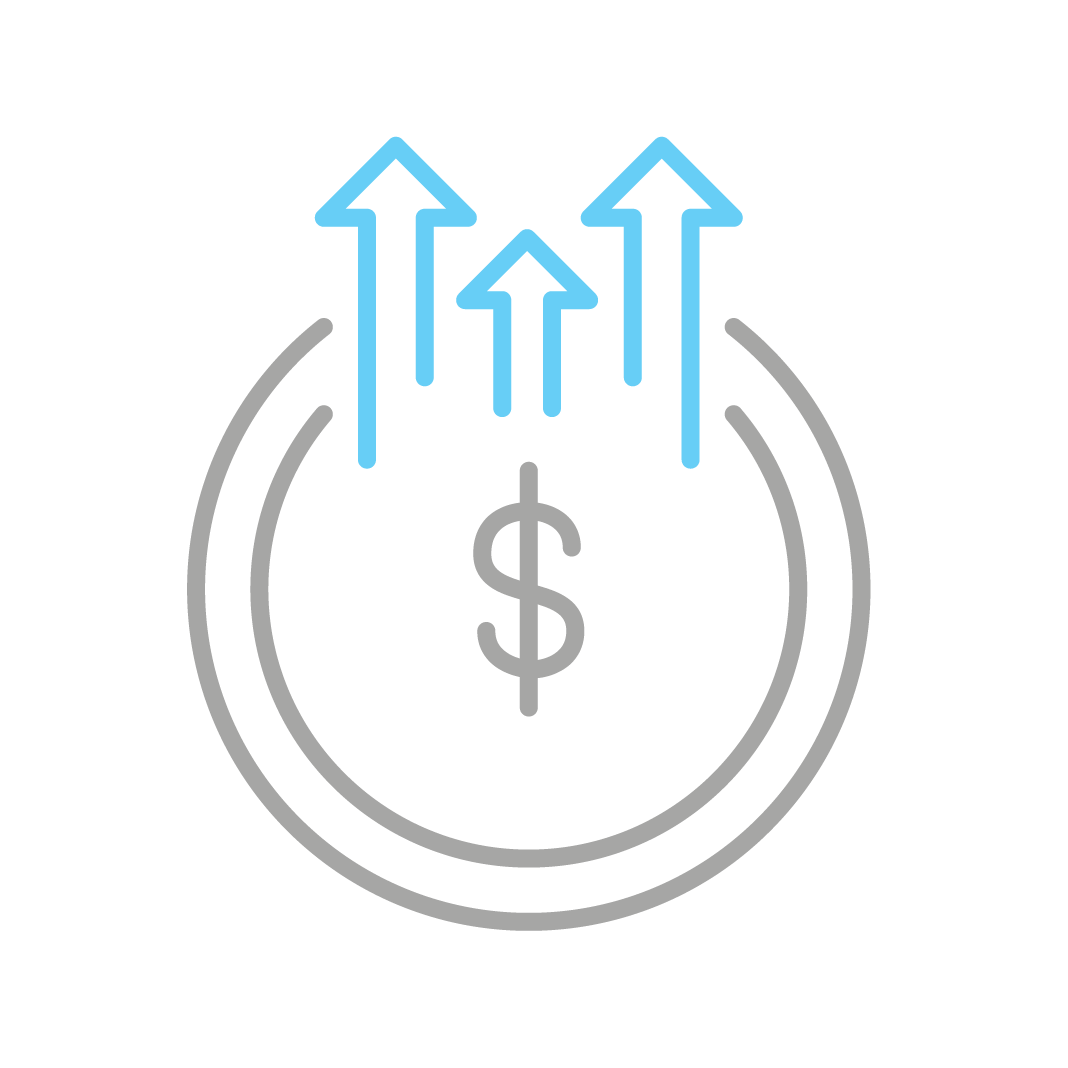
HIGH INVESTMENT COSTS
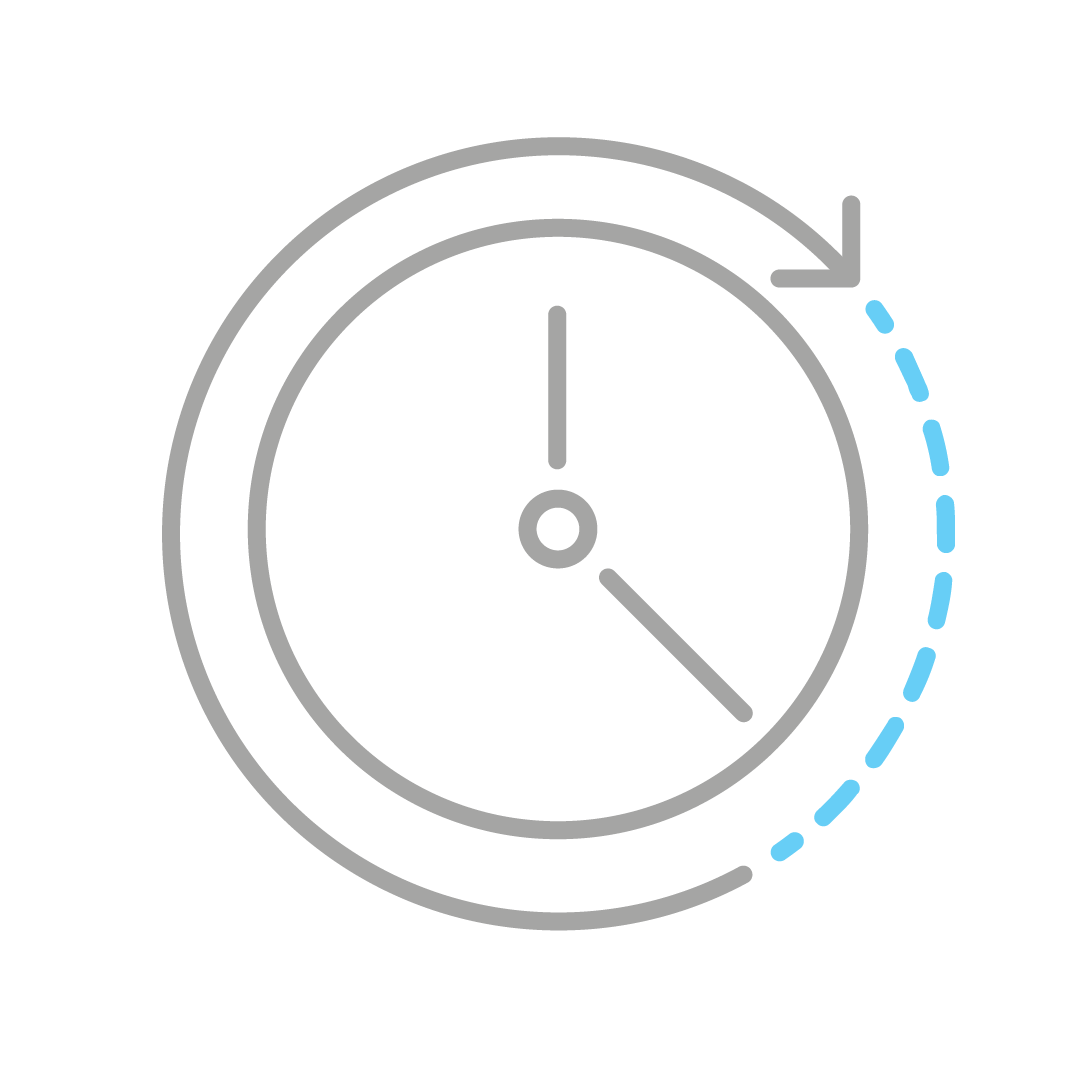
LONG PRODUCTION RAMP-UP
SOLUTION
3D printing (additive manufacturing) is an agile production method and one machine can produce several different parts, enabling small quantities to be produced cost-efficiently and quickly. Additive manufacturing does not require extensive preparation and the production of costly tools and molds. It shortens development processes through rapid design iterations. With on-demand production even small quantities can be created without high risk.
Using the Replique platform you can leverage existing 3D printing design and material expertise and capacities of a worldwide production network. By connecting our platform into your existing ordering channels such as e-commerce and ERP systems, everything works as usual, only much easier!
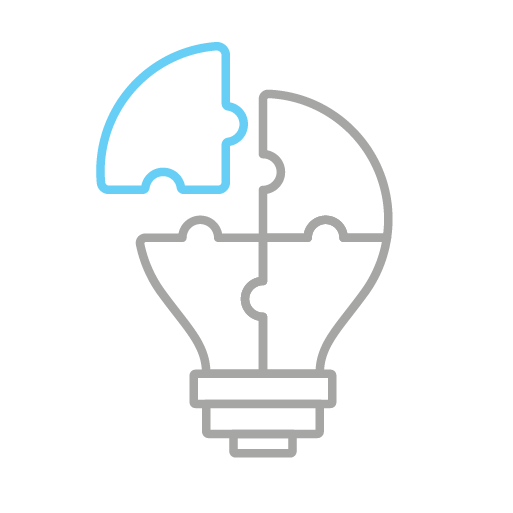
MORE INNOVATION
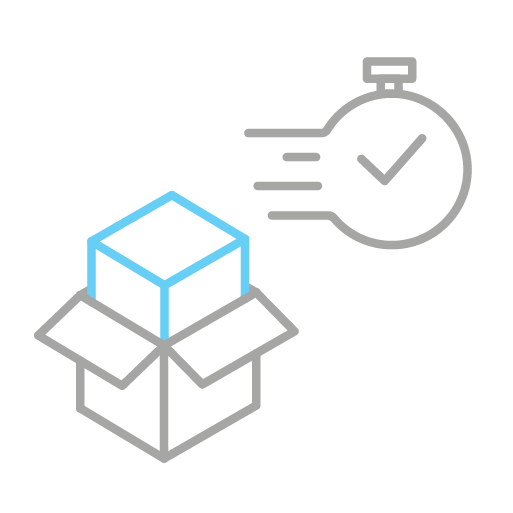
FASTER GO-TO-MARKET
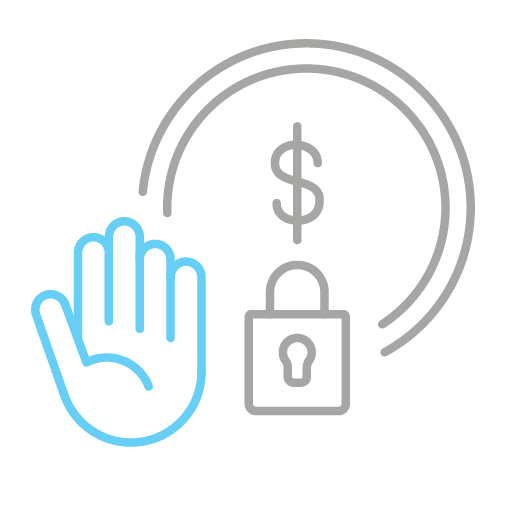
CLOSE TO ZERO FIXED COSTS
SMALL SERIES USE CASES
Additive Manufactured Doorstopper for Alstom
How Alstom benefits from our services:
- Support for design iterations to generate final prototype
- Material and technology selection for cost efficient production
- Qualification for serial production
- Lead time reduction
- Fulfilment and shipment via network
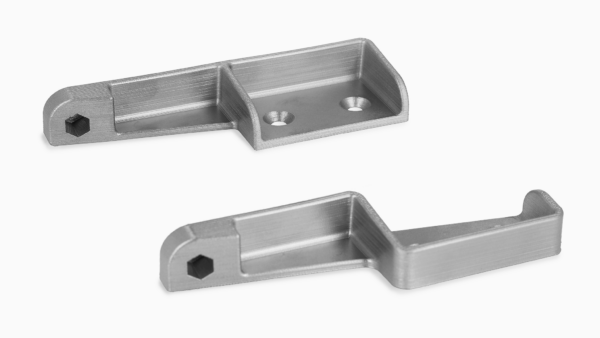
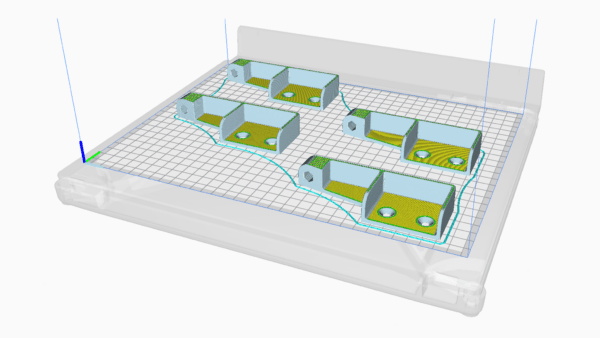
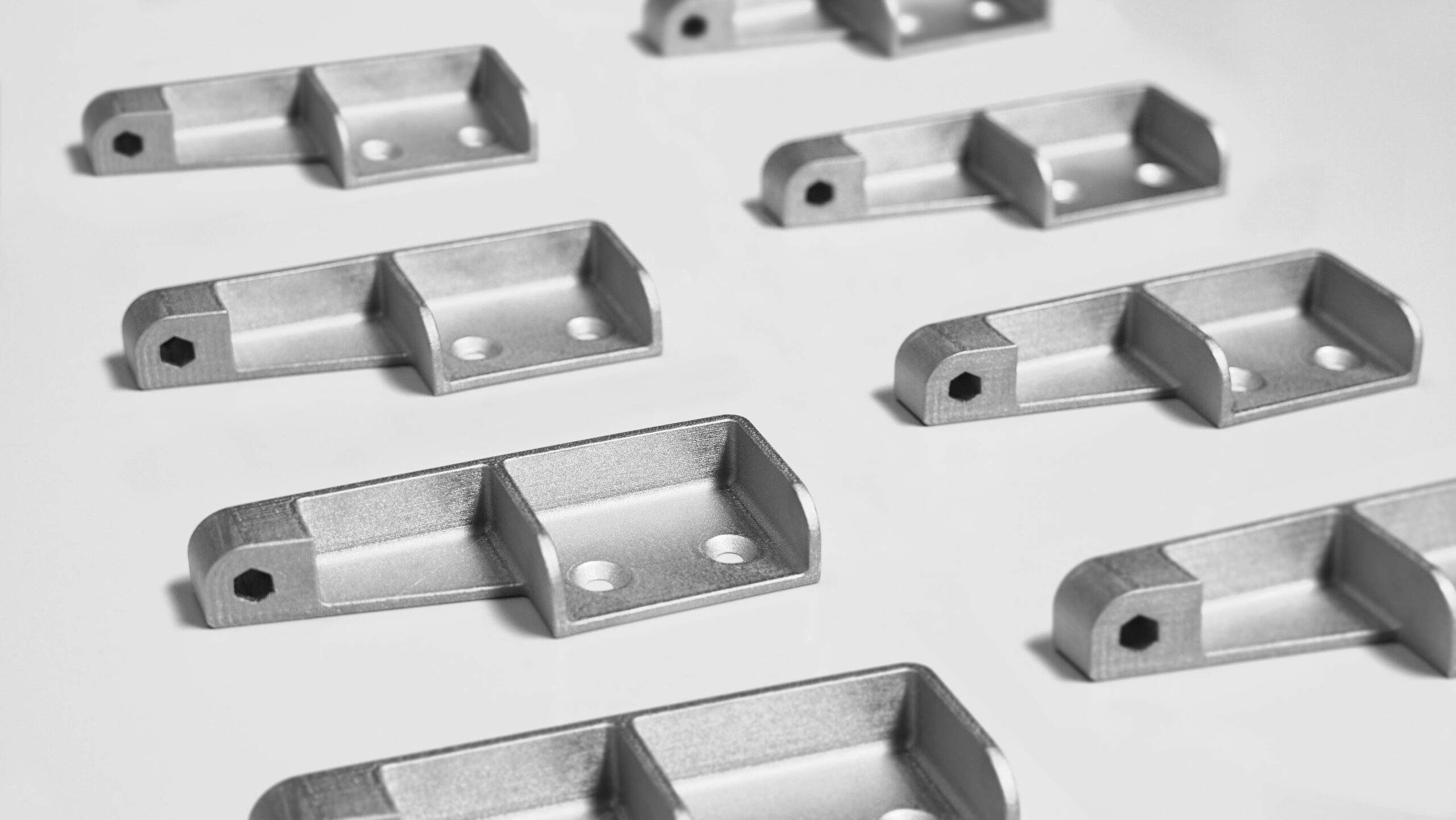
With Replique, we benefit from all major additive manufacturing technologies and materials from a single source. In addition, we receive optimal technological preparation.”
– Ben Boese, former 3D Printing Hub Manager of Alstom Transport Deutschland GmbH.
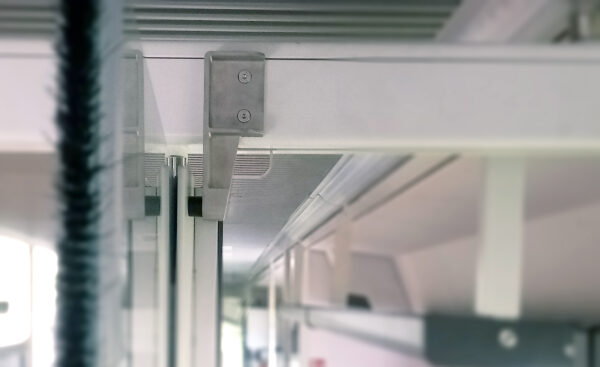
3D Printed Borehole Cleaning Aid for Miele
How Miele benefits from our services:
- Setting up production parameters for 3D printing
- Material and technology selection
- Production according to GMP (Good Manufacturing Practice)
- Miele webshop integration
- Order fulfilment and shipment via network
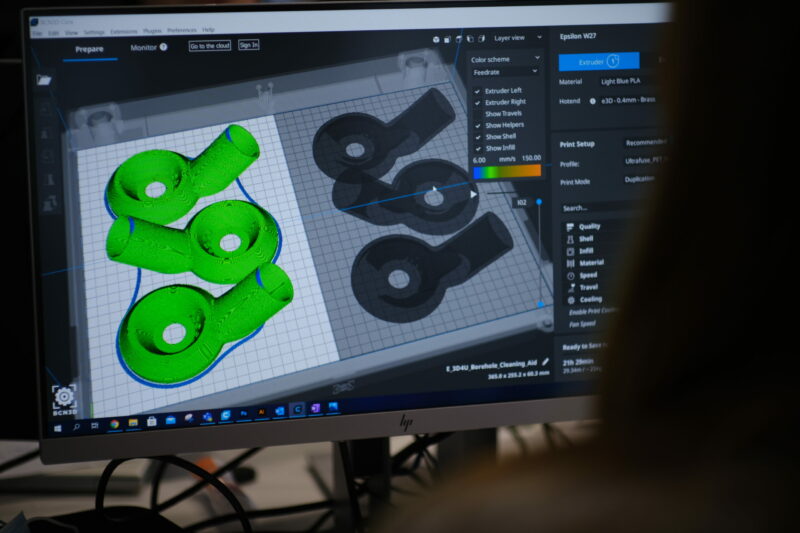
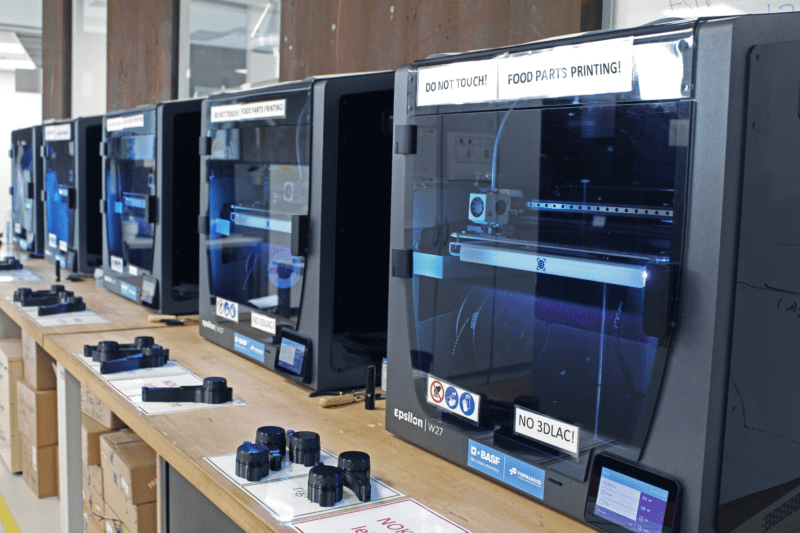
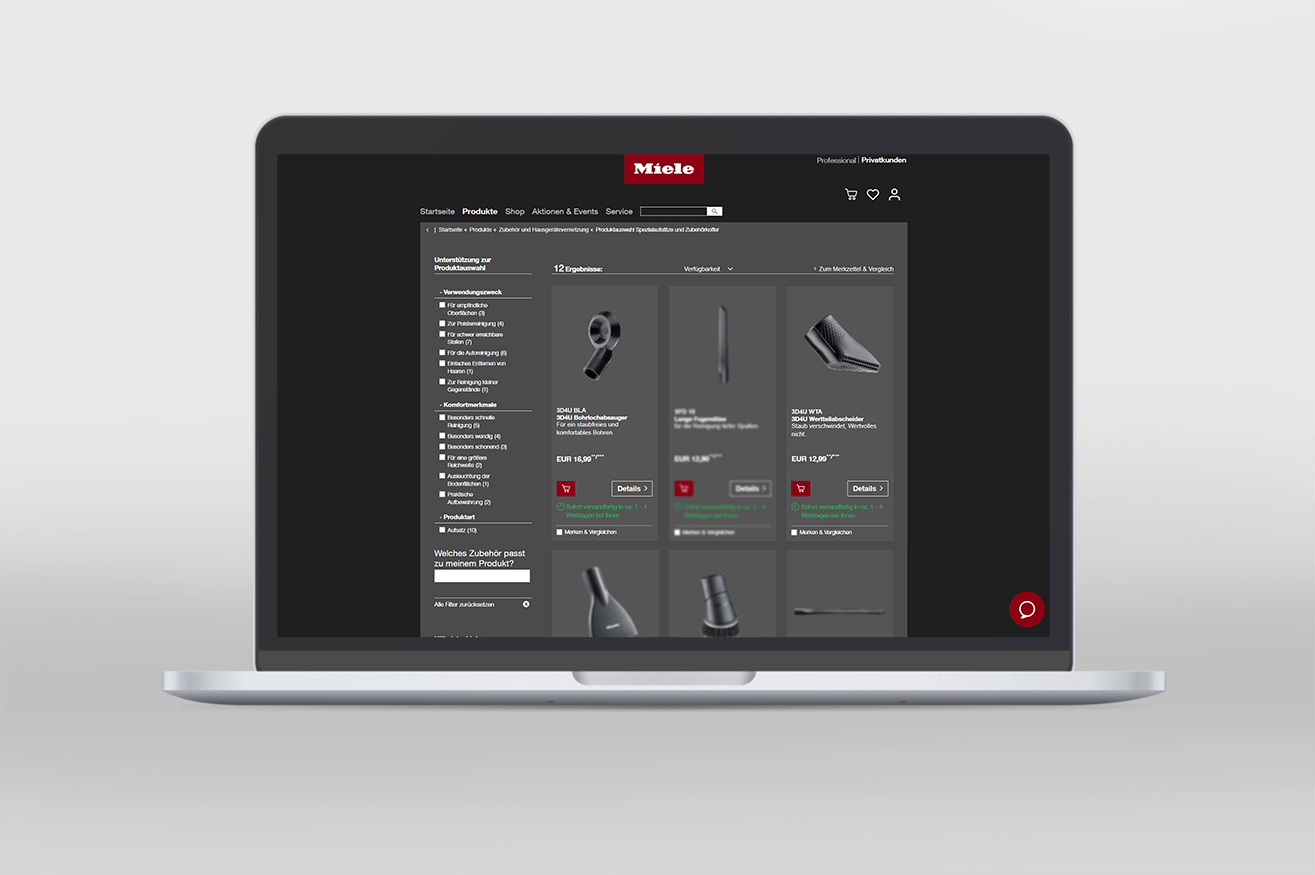
As a one-source partner Replique provides parts in industrial grade quality over a worldwide network of qualified 3D printing service bureaus.
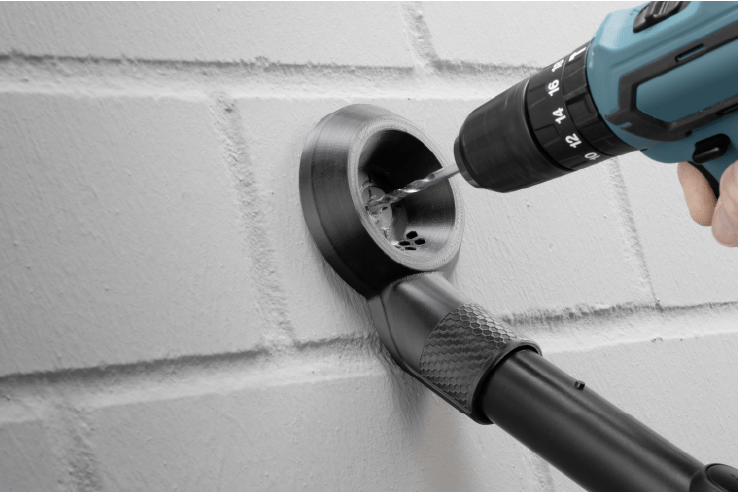
Customized Wheelchairs for RehaMedPower
How RehaMedPower benefits from our services:
- Part screening, resulting in 17-23 3D printed parts within the wheelchair
- Material and technology selection
- Production via trusted AM service provider
- Reduced development time by 30%
- Reduced development costs by 60%
- Shifting from prototyping to serial production with on-demand parts
- Easy integration of spare parts possible
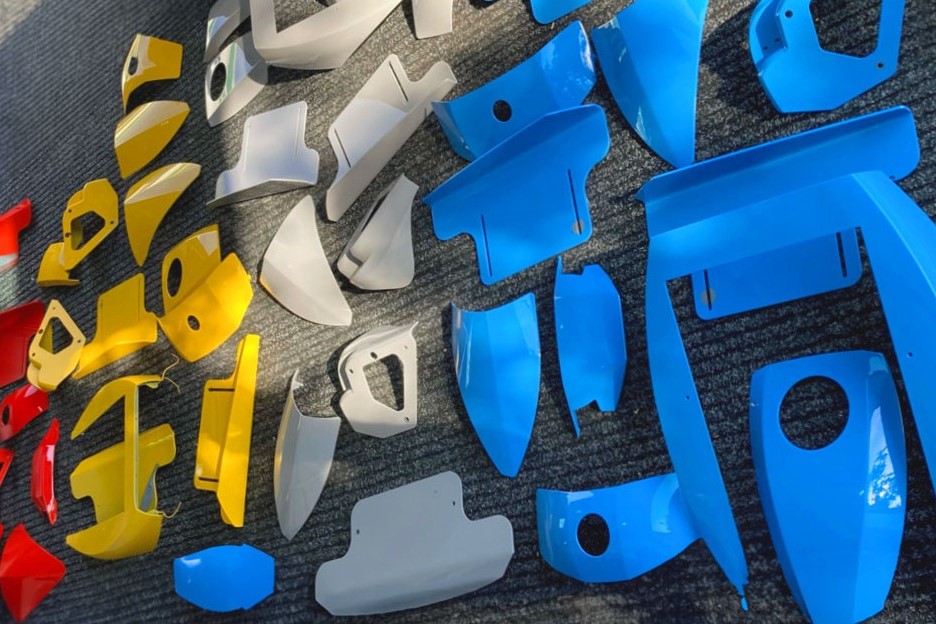

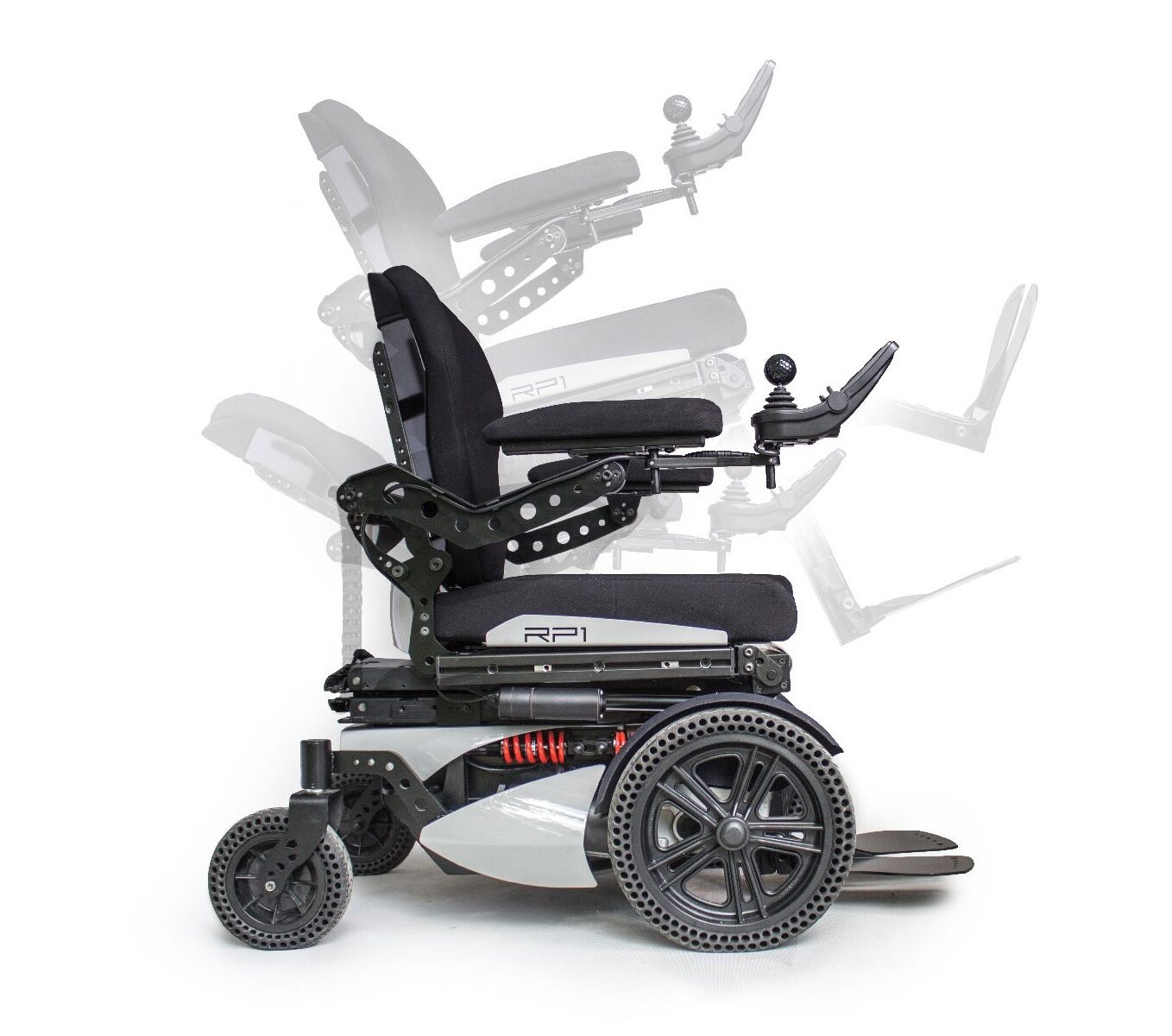
“Teaming up with Replique also offers some crucial benefits, such as flexibility in demand planning with production on-demand and the ability to implement changes rapidly and offer special parts to meet the individual needs.”
– Thyl Junker, Head of Development at RehaMedPower
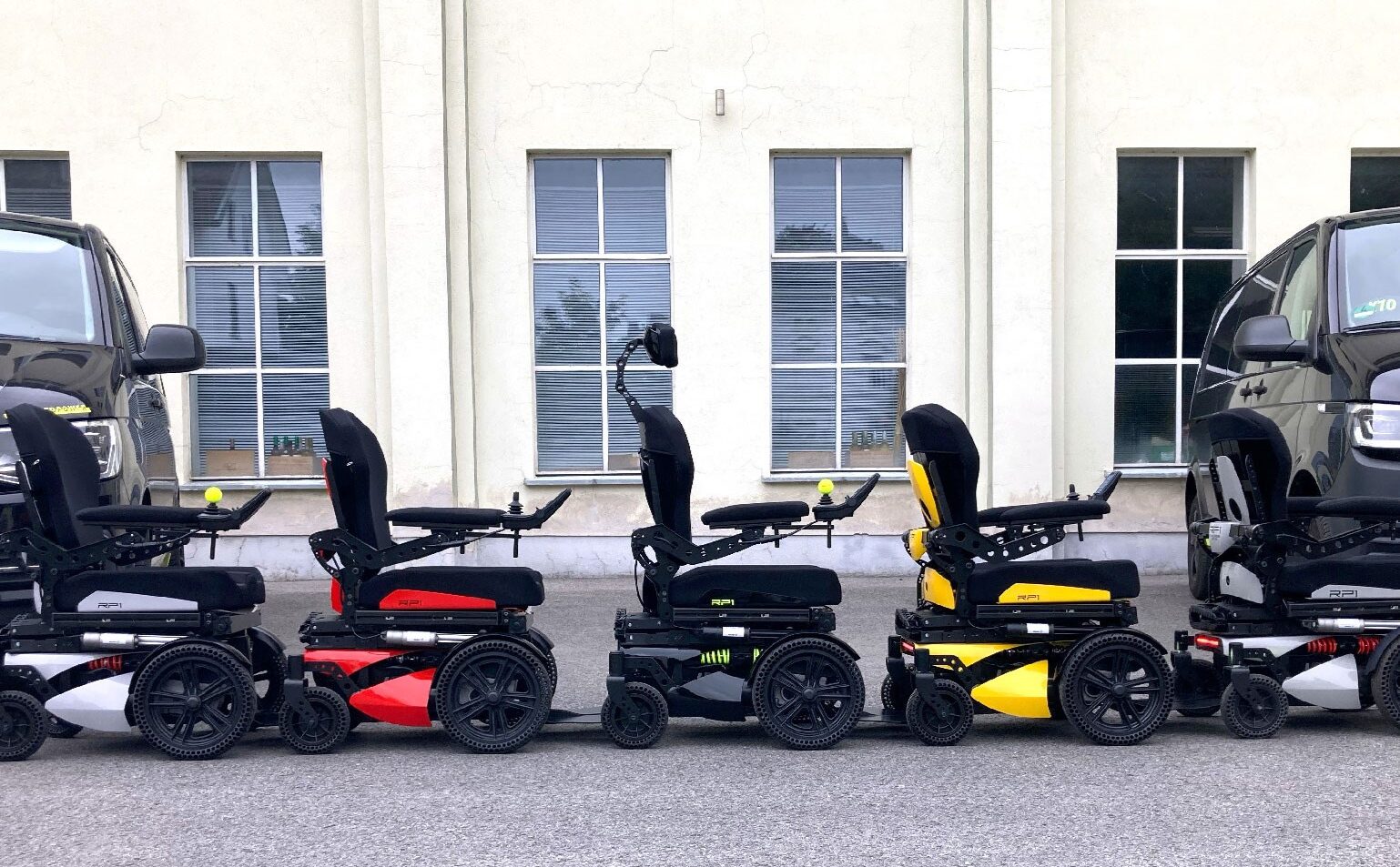
HOW YOU CAN BENEFIT FROM OUR 3D PRINTING SERVICES FOR SMALL SERIES
- 3D-scan services
- CAD construction and design for 3D printing
- Material and technology consultation
- Generation of printing parameters
- Digital warehousing
- Decentral production using our worldwide 3D printing network
- Purchase quantity starting at lot size 1
- Connection to ordering channels such as e-commerce stores or ERP systems
- One-stop-shop, no previous 3D printing experience required
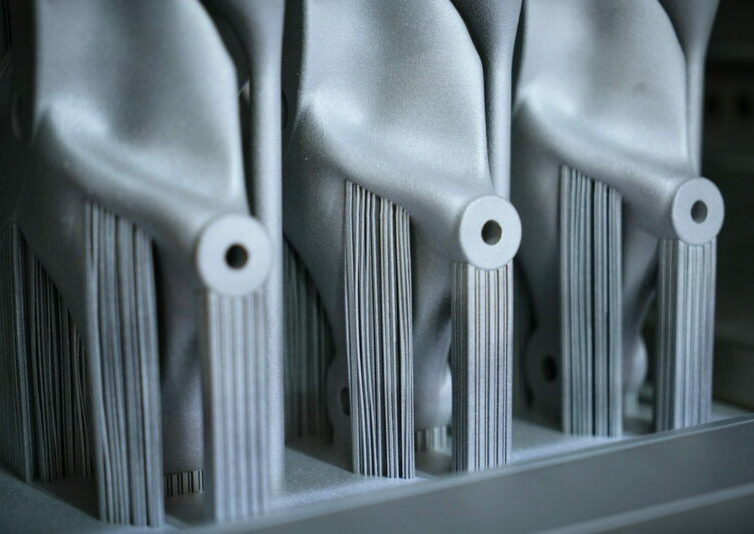