MAN Truck & Bus leverages Replique’s 3D printing platform for efficient spare parts manufacturing
Mannheim, November 28, 2023 – MAN Truck & Bus, a global leader in transport solutions, is embracing 3D printing through Replique’s production platform to manufacture spare parts on-demand, locally, and without the need for physical inventory. Starting with the production of bronze manifolds for the cooling water supply of a marine engine, MAN aims to undertake further projects in the future to reduce costs and further optimize service.
Challenges in Spare Parts Management
In special machine construction, ensuring spare parts supply is often challenging. Small quantities, unpredictable consumption, and sometimes lengthy delivery times typically require stocking critical components to avoid costly equipment or machine downtimes.
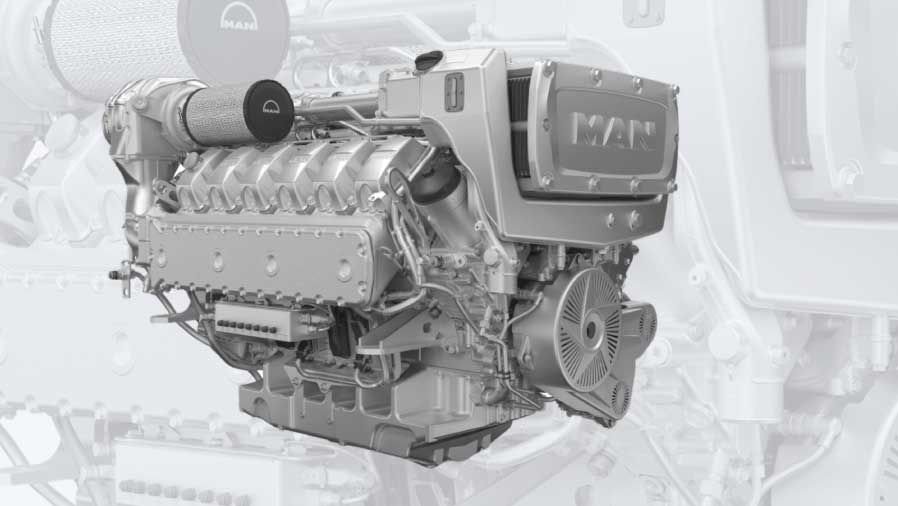
In a recent case, MAN faced the challenge of urgently having to acquire 10 bronze manifolds for the cooling water supply of a marine engine that were no longer in stock. The casting mold for this critical component was unavailable. Conventional procurement methods involving the creation of models, casting, and mechanical machining would have been both time and cost-intensive. MAN, therefore, sought an alternative solution to meet the short-term demand, one that also met the high technical requirements for this highly stressed component.
Efficient Spare Parts Management through On-Demand 3D Printing
Collaborating with Replique allowed MAN to reproduce the 10 manifolds in original quality using additive manufacturing – all that was needed was a 3D model and a manufacturing drawing. In collaboration with its material partners, Replique selected a material (m4p™ Brz10) that was technically equivalent to the original material. Production took place through Selective Laser Melting (SLM) via a local 3D printing service from Replique’s network of more than 85 partners worldwide. From MAN’s initial inquiry to the delivery of ready-to-install parts, only about 7 weeks passed. Tensile tests conducted at MAN’s Central Material Technology department revealed that the chosen material actually exhibited better technical properties than the original. The use in practice of these parts was also successful, leading MAN to place an additional order for 10 units.
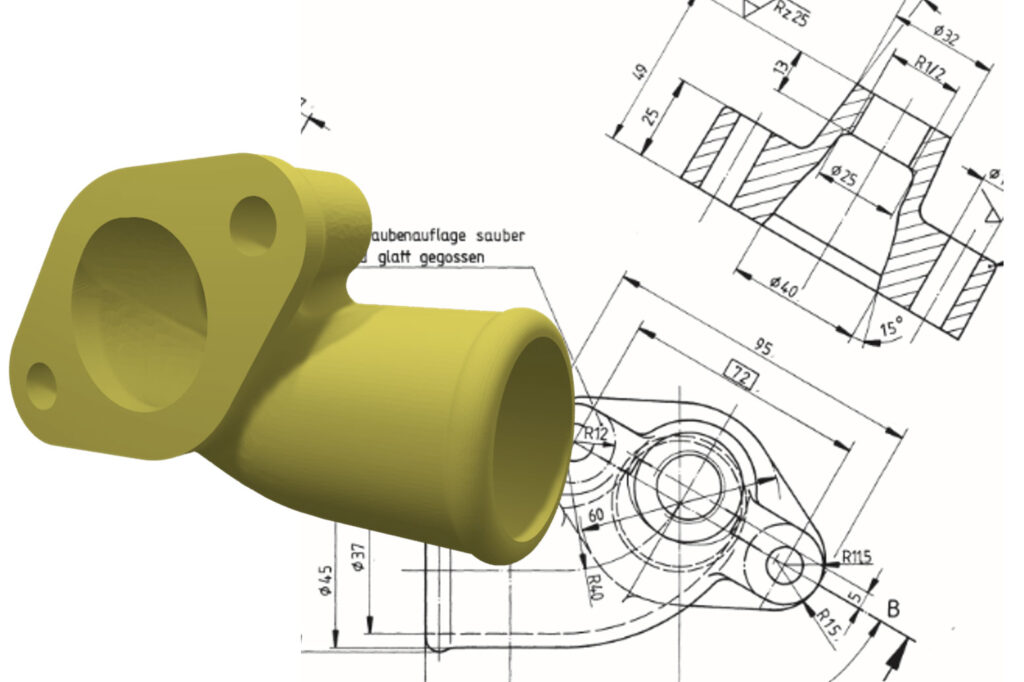
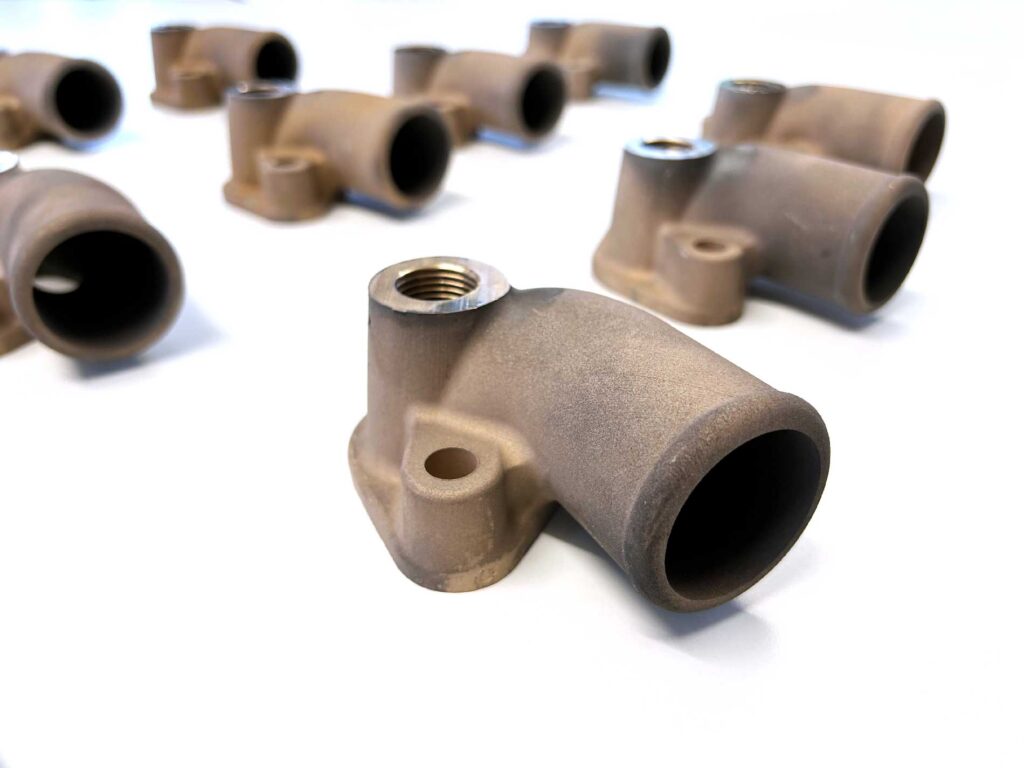
The 3D printed bronze manifolds surpass the requirements of the original part. Due to the digital availability of production information, they can be reordered at any time with consistent quality.
As the relevant component has already been qualified for 3D printing and a corresponding print file is created and digitally available, including information on the used material and technology, the manifolds can be reordered at any time in consistent quality. MAN incurs no fixed costs for molds and models or storage costs, resulting in attractive overall costs per unit for small quantities.
“The collaboration with Replique was seamless from our initial contact to the moment we received the finished parts. It allowed us to promptly assist our spare parts customers, and we are already in the process of realizing another 3D printing project with Replique,” says Thomas Hauck, Spare Parts Logistics MAN.
“The use of additive manufacturing enables companies to overcome traditional production challenges. We are happy to work together with MAN to ensure a reliable and efficient supply of spare parts in the transport and marine sectors,” says Dr. Max Siebert, CEO and Co-Founder of Replique.
Related Posts
Categories
- 3D printing industries (6)
- 3D Printing Materials (1)
- Basics (3)
- News (1)
- Point of View (10)
- Press (20)
- Press (20)
- Sustainability (3)
- Technology (6)
- Uncategorized (1)
- White Paper (1)