How to manage supply chain disruptions with additive manufacturing
Without a doubt you have at least once in the last few years struggled to find and purchase a consumer good. Be it toilet paper, a bike or within the last month furniture from a certain large Swedish company – supply chain disruptions affect all of us. Political conflicts, trade policy laws, complex custom processes or natural disasters. These challenges and more can weaken supply chains extremly. However, with the outbreak of the COVID-19 pandemic, supply chain disruptions have reached new heights. Factory shutdowns (especially in Asia) as well as the widespread lockdowns have led to disruptions across logistics networks, significantly increased freight prices and lead to unbearable long delivery times.
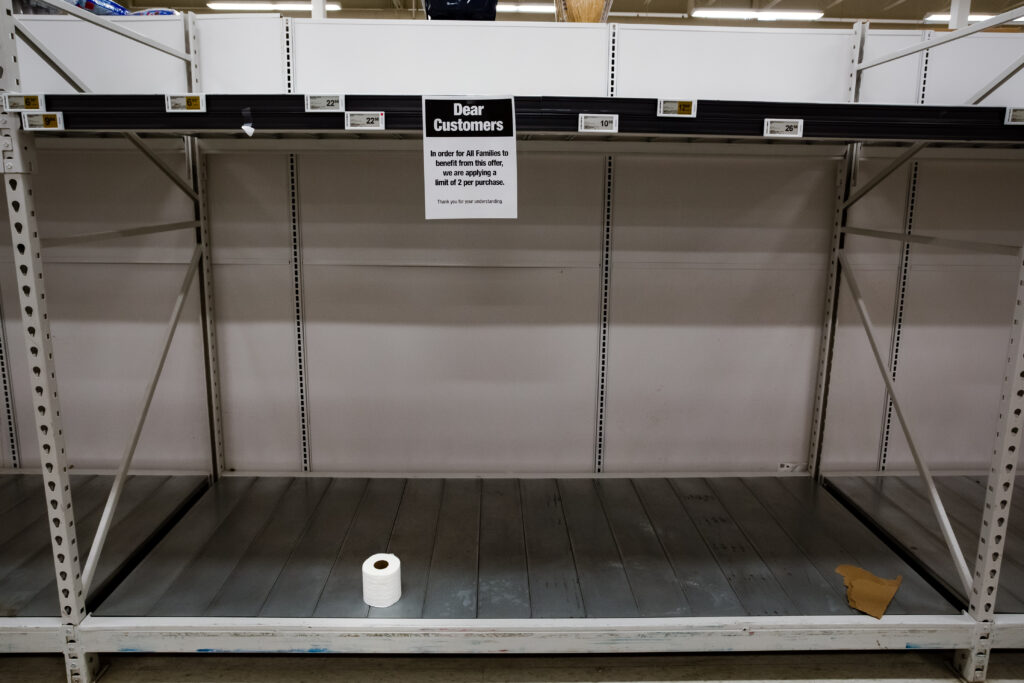
Big companies tend to focus on just-in-time production as it certainly increases efficiency and comes with huge savings regarding inventory costs. Parts are often produced on the other side of the world and shipped to a central warehouse – just-in-time. However, it became visible that this strategy is no longer suitable – at least not for every item. We need to become aware that such disruptions are the new norm. They are part of our globalized supply chains. So how can supply chains become more resilient? In this blog we want to dive deeper into the topic of supply chain disruptions and propose a solution that could enable higher availability of your parts.
The effects of disruptions on the global supply chain
The shown examples don’t convince you yet? Here another one: Only one stuck ship in the Suez Canal for six days in 2021 led to a delay of 9 to 14 days of around 390 ships. This led to 13 to 14 million $ of revenue loss per day. And on top of that freight prices and transport costs were rising significantly. The incident especially affected the automotive industry, however other industrial sectors struggled as well.
The high relevance of supply chain disruptions is also seen within recent movements. For example, the New York FED started a new Barometer of Global Supply Chain Pressures, as seen below. In this barometer, called the Global Supply Chain Pressure Index (GSCPI), they integrate several commonly used metrics to provide a more comprehensive summary of potential supply chain disruptions.
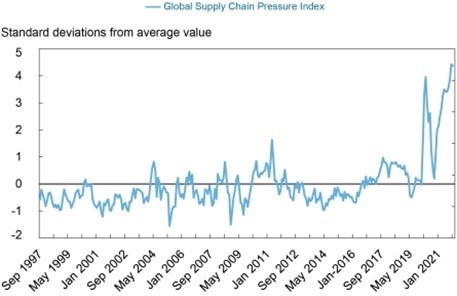
The graph shows the overall global supply chain pressure and it’s up and downs. During 2011 e.g. the index is rising with two huge natural disasters – one being the Tōhoku earthquake and resulting tsunami, impacting both Japanese and foreign production, as the affected regions were the center of the automotive industry. The other event was the flooding in Thailand, affecting global supply chains of the automotive and electronics industry. And, of course with the outbreak of COVID-19, the index rises sharply. When production went back in summer of 2020, it shortly fell, however since then it has risen again at dramatic pace. The chart clearly shows how vulnerable current supply chains are and call out for a solution apart from traditional methods.
Long delivery times negatively affect customer satisfaction and sales
We also see these supply chain issues within our customer base and some of them might have to wait up to two years to get a specific traditional material. In general, the lead time in traditional manufacturing for reordering a part takes around two to three months, which is already a significant duration, if for example a spare part is urgently needed by a customer.
This has a big impact on overall customer satisfaction and can decide if a customer is going to reorder from a certain company or not. Despite a bad reputation of the company, it can also lead to huge costs for the customer, and maybe even to penalty costs for the manufacturer. Only a single part missing can cause a halt of production for weeks. Looking at the fact that 1 minute of downtime in the automotive industry for example can cost between 22.000 to 50.000 $, this is something that has to be avoided by all means. So how can supply chain disruptions be prevented?
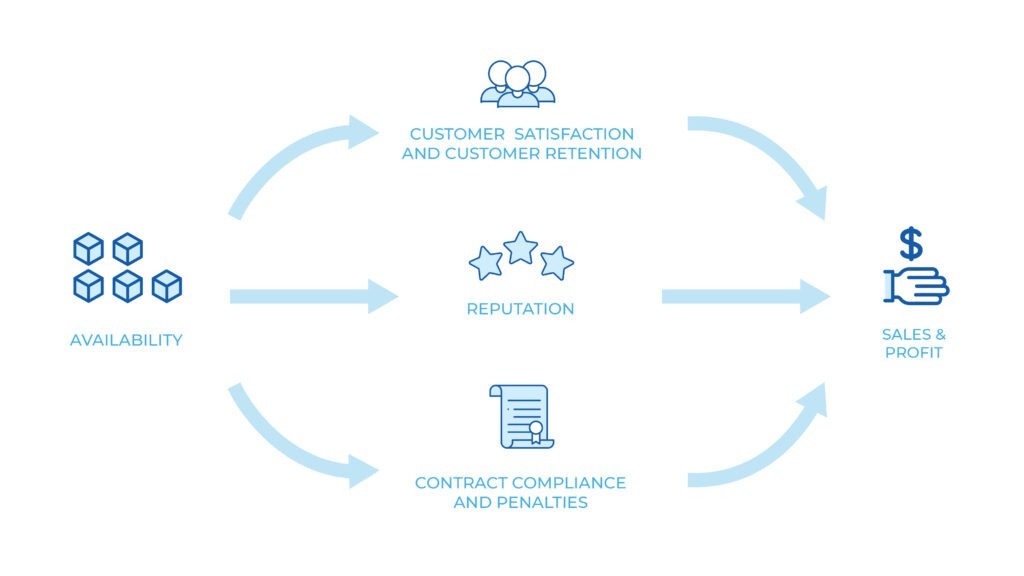
Additive manufacturing solves supply chain shortages being an agile production method
Traditional production methods are inflexible. It takes a long time until a needed part can be replaced. Supplier lead times are long, a tooling has to be created and costs for production in low volumes are just too high.
3D printing however comes with a new and agile approach. A machine can produce all kinds of parts, just with the translation of a design into a 3D printable file. Production can work on-demand: after the preparation of the file, only printing time and – if necessary – post processing time have to be accounted for the lead time. By this, lead times can be reduced from around 3 months to just hours if the part is printed directly in the production center. This certainly is a huge benefit when spare parts are urgently needed. Moreover, additive manufacturing can be done decentral, mitigitating supply chain risks to a maximum.
The best way of integrating 3D printing depends on the use case
There are several ways of how additive manufacturing can be integrated into company processes. The manufacturer could print the part in a central print farm in-house and store it in a physical inventory, until a customer needs it, or just produce it centrally and send it to a customer on-demand. This approach however would not change current processes much, just think of long custom processes.
Another possibility would be a rather digital approach. Instead of sending the physical part, the company sends the 3D design to the customer. The customer then prints the part by themselves. This would eliminate waiting times and shipping costs. However, it assumes that the customer has the infrastructure and knowhow to print the needed part.
The most flexible and secure way would be to use a decentral network of 3D printing service providers. However with this approach a new challenge is coming up: How do OEMs know which production partner is trustworthy? And how can files be sent in a secure and encrypted way? Replique solves these new challenges with a trusted manufacturing network and a digital inventory platform where all part designs can be stored in a secure way. Once an order comes in, an additive manufacturing partner of Replique’s network fulfills the order on-demand and sends the printed part directly to the customer. The huge benefit lies in the encryption of the file transfer, making sure that the part design stays in the right hands. Moreover, the part can only be printed with the print parameters that were defined beforehand. By this, it is assured that all parts created have the expected quality.
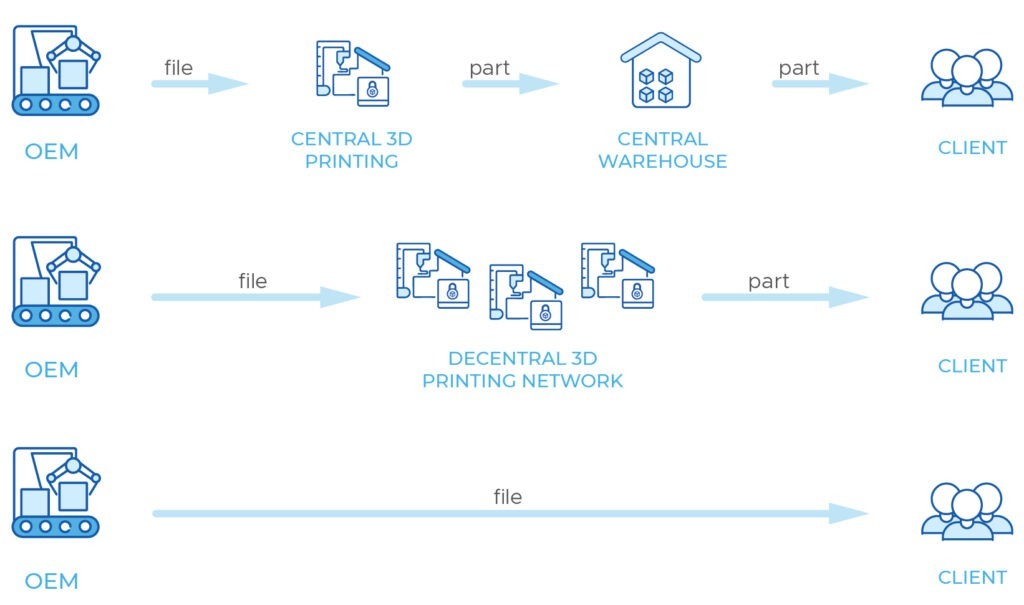
Conclusion
Supply chain disruptions are already occurring since several years. However, with the rising globalization and other more emerging problems such as natural catastrophes (also due to the ongoing climate change) and pandemics, the challenges become bigger. Luckily, with problems growing, new and innovative solutions are paving their way. Additive manufacturing as an agile production process enables the production on-demand and at the place needed. A digital inventory allows the secure storage and file transfer of the 3D designs. Finally, 3D printing can overall reduce supplier dependencies and enables a flexible and resilient supply chain approach.
Do you want to learn more about the topic and find out how 3D printing can improve your supply chain efficiency? Contact us and we can schedule a call!
Download our free whitepaper for a full guide to supply chain resilience
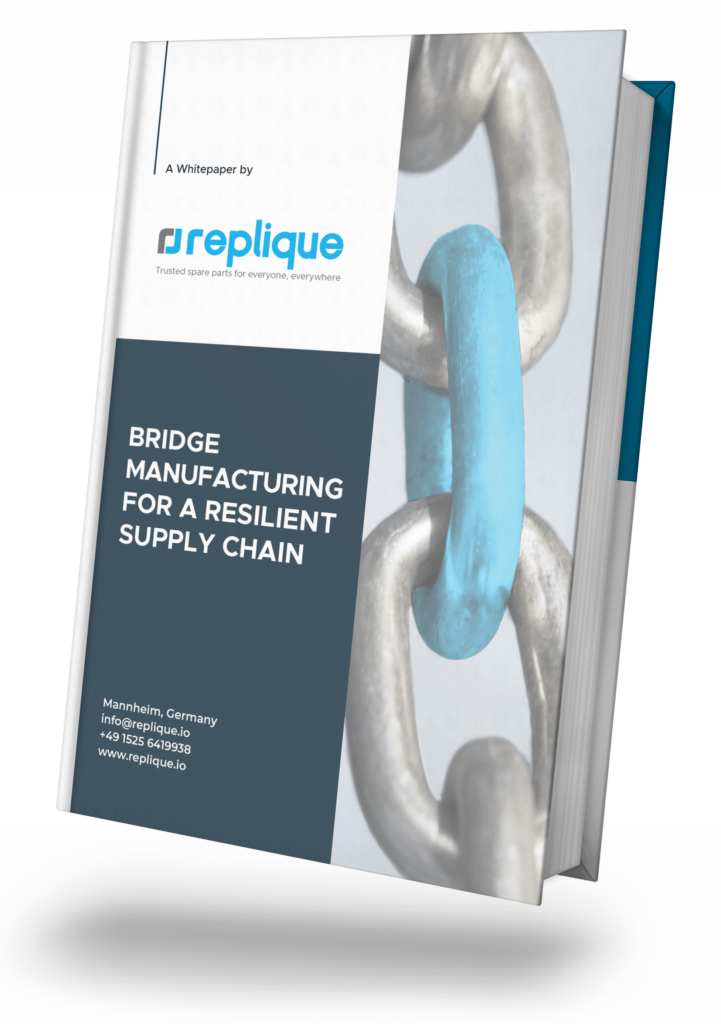
Categories
- 3D printing industries (6)
- 3D Printing Materials (1)
- Basics (3)
- News (1)
- Point of View (10)
- Press (20)
- Press (20)
- Sustainability (3)
- Technology (6)
- Uncategorized (1)
- White Paper (1)